NEW TRACKER HELPS PEOPLE SPOT AND ELIMINATE HAZARDS
[December 13, 2022] More Bright Wood people can see their workplaces with OSHA’s eyes thanks to a new application called the Hazard Tracker. “The tracker is a great teaching and training tool,” Jim Sanders, Madras Safety Manager, said. “You can see what issues OSHA will have. You can also learn how to abate hazards by seeing what other people did.”
OSHA Looks for Hazards
Jim accompanied an OSHA inspector during a comprehensive inspection in 2021. “We physically inspected every nook and cranny in Madras,” Jim said. “We went through all 16 production facilities, offices, and every support entity and building we have. It was two weeks of 10-hour days.”
“The inspector opened my eyes to issues I thought were normal and part of doing business,” Jim said. “I learned a lot about what you need to do to comply. The Hazard Tracker is a way to pass on that information to as many people as possible.”
See the Hazard, See the Fix
“The Hazard Tracker has proven helpful in many ways,” Laci Brown, Redmond Safety Manager, said. “It allows the user to keep track of the different hazards and recommendations. Before and after photos show how we resolved an issue. All the sites can see each other’s resolutions and improvements and utilize the same ideas.”
“We shouldn’t be reinventing any wheels now,” Daryl Booren, Personnel Director, said. “We have this great tool to look at comparable hazards and how they were abated. Most importantly, it has a picture that tells the story: Here was the hazard; here is the abatement.”
“Bright Wood has a lot of facilities and variety, but we also have a lot of commonalities and similarities,” Daryl said. “The end plan is to make the Hazard Tracker accessible to everybody, so someone in Prineville can quickly see how Redmond guarded a saw and vice versa.”
One Umbrella for Safety
The Hazard Tracker is one component of the new Incident Tracker 3.0 developed by Dan Wright of Bright Wood’s Information Technology (IT) department. “The Incident Tracker 3.0 tracks all of our injuries, property damage, and near misses,” Jim said. “Whenever something happens, an incident has to be created within the system. And then, a safety committee member and their supervisor investigate what happened and get all the details. If a hazard is found, it is entered into the Hazard Tracker and it is up to management to abate it.”
The Incident Tracker 3.0 mirrors that process with three separate tabs of information: 1) incidents, 2) investigations of incidents, and 3) hazards. While only safety managers and safety committee members will have access to the first two tabs, everyone at Bright Wood will one day be able to search the Hazard Tracker.
“Dan pulled the whole package together and wrapped it up nice and neat for everyone to access,” Daryl said. “He has put in hundreds of hours to create an intuitive application so everybody can utilize the system and get out of it what they need to make the workplace safer and compliant.”
The Goal Is Preventing Injuries
“I can’t say enough about how visual the Hazard Tracker makes it,” Jim said. “It is out on the table, you can see it, and it doesn’t go away. In the end, all we are trying to do is prevent injuries.”
A Better Tool for Resolving Hazards
The Hazard Tracker makes it easier for managers to resolve issues. For instance, a list of the hazards assigned to a manager pops up every time they open the tracker. Color coding signals which hazards to work on first, and a to-do list covers exactly what needs to be done.
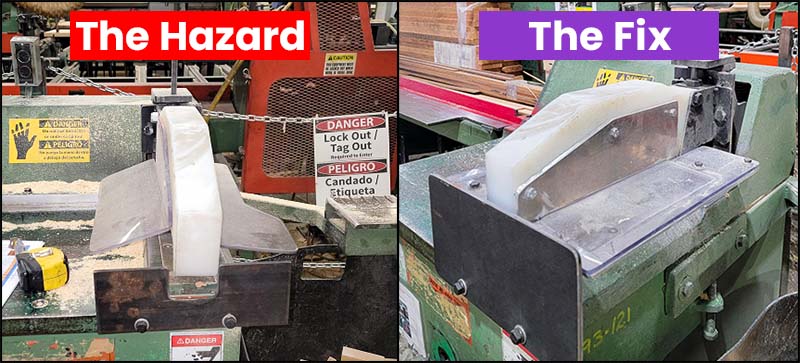
The Hazard: This chop saw guard in the Redmond Lamination Plant was inadequate because people could still get their hands and fingers underneath it.
The Fix: Support Services installed a new guard, which blocks entry to the danger zone and is easier to adjust.
The Takeaway: Do you have any guarding that could be better?
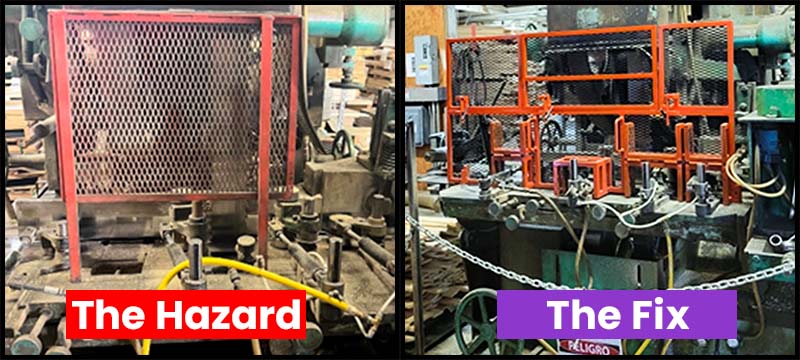
The Hazard: The guard left too many openings for people to access the Ferrari saw’s blade.
The Fix: The Fabrication Department built a custom guard that completely blocks access to the saw.
The Takeaway: Do you have any guards doing an incomplete job of protecting people?
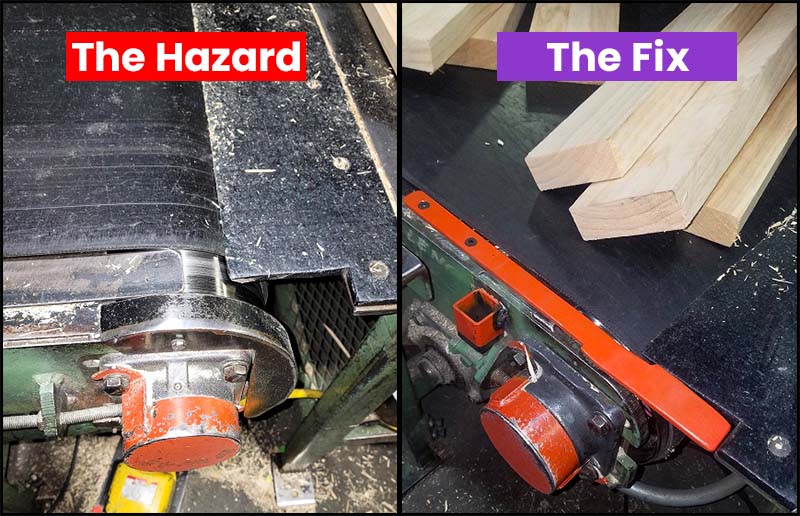
The Hazard: People could potentially catch their hands or clothing in this moving cutstock belt in Redmond’s Cut Plant.
The Fix: Bright Wood’s Fabrication Department built a guard to block access to the nip/pinch point.
The Takeaway: Are there any moving parts in your work area that should be guarded?
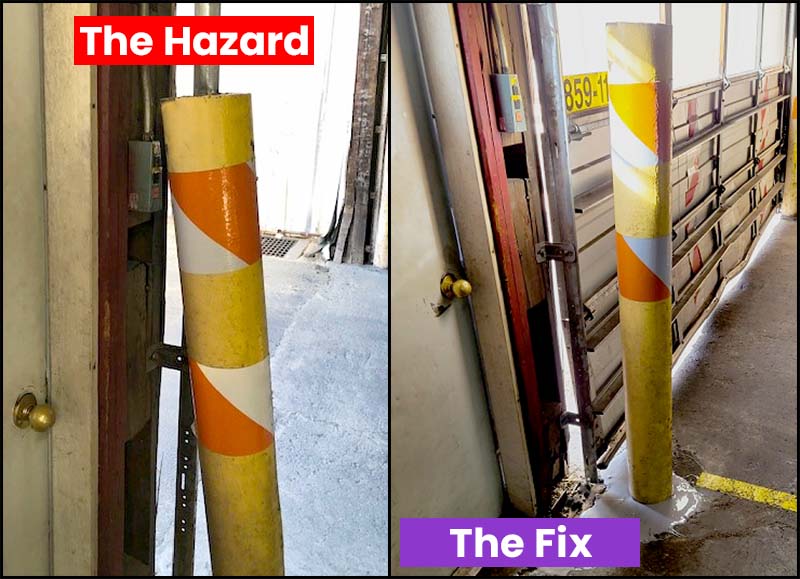
The Hazard: A forklift damaged this yellow safety pole in the Redmond Cut Plant. The pole must be upright and sturdy to adequately protect the door and pedestrians from harm.
The Fix: Maintenance reset the pole, so it is strong and stable.
The Takeaway: How many safety features in your plant are damaged or neglected?